The inspectors in the NCDA&CS Fuel Quality Section conduct unannounced routine inspections at locations within their territories with the goal of inspecting every station at least once during the calendar year. When conducting a routine inspection there are three primary areas that the inspector focuses on:
- The labeling on the fuel dispensers
- The quality of the fuel through the dispenser
- The quality of the fuel in the storage tank
Inspectors routinely check the labeling on fuel dispensers to verify that they clearly identify the product that the consumer is purchasing. Additional labeling may be required for certain blended fuels and for dyed fuel products. Below is a list of required labels our inspectors are looking for:
- Registered brand name (gasoline, ethanol blends, ethanol flex fuel, diesel, biodiesel, biodiesel blends)
- Grade of fuel (gasoline, ethanol blends, ethanol flex fuel, diesel, biodiesel, biodiesel blends)
- Ethanol label (fuels that may have over 1% ethanol, ethanol flex fuel)
- Biodiesel % (diesel fuel with greater than 5% biodiesel, other biodiesel blends, B100)
- Suitable use sticker/Dye (Kerosene)
What happens if a problem is found with a label? The inspector will typically issue NOV and give 2 weeks to resolve issue, unless there is no labeling at all. If the problem is not fixed in a reasonable amount of time the dispensers can be closed until resolved.
Our field inspectors work out of a mobile laboratory that allows them to complete the following quality tests while onsite at a retail location. Inspectors can perform the following tests on the fuels below. Problems found regarding the quality of fuel usually results in an immediate stop sale of the product, with a passing inspection being needed before sales can resume.
Gasoline
Octane – The octane number (also known as the anti-knock index or AKI) is a measure of a gasoline’s ability to withstand autoignition. Under the right temperature and pressure conditions, the air-gas mixture within the engine cylinder can ignite ahead of time. This combustion results in an audible knocking sound in the engine and can reduce engine efficiency. This “engine knock” can potentially lead to engine damage if allowed to continue over a long period of time. The higher the octane number of the fuel, the more resistant the fuel to this auto ignition. Please note – using a higher octane fuel in an engine that is designed to use 87 octane gasoline will have no appreciable effect on the performance of that engine.
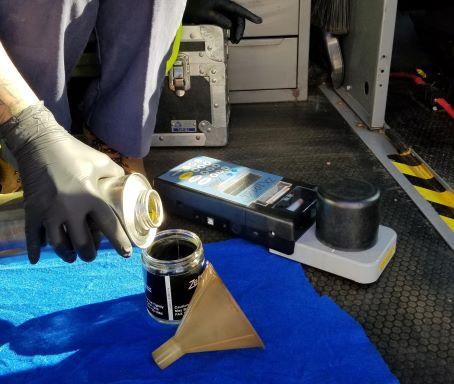
In the field inspectors use a portable octane screener that utilizes near infrared light to analyze fuel samples. The spectrum of the sample is compared to a calibration curve derived from samples tested using the octane engines in the lab to give a predicted octane value. If the value of the gasoline sample is determined to be below that of the posted octane number, the sample is submitted to the central laboratory for further analysis using the engines.
Distillation – This test provides information regarding the fuels volatility or ability to be vaporized. This test is conducted by boiling the fuel and measuring the temperature of the distillate at different points during the test. The final distillation end point (or final boiling point) is one of the most important data points that is collected during this test. An elevated end point is the result of the fuel being contaminated with a higher boiling fuel such as diesel or kerosene and can lead to a vehicle engine shutting down.
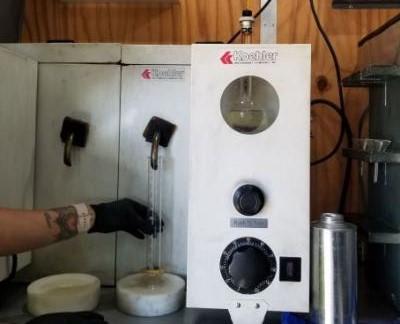
Percent Ethanol by Volume – The volume of ethanol in gasoline is required by law to be displayed on the dispenser and is limited to specific volume ranges based on engine type. In the field, inspectors test gasoline products that have between 0% to 83% by ethanol volume to verify that these fuels meet the required specifications.
Water and Sediment – Water is the largest concern for consumers when it comes to fuel quality as its presence can result in poor engine performance and possible failure. Sediment can result in clogged fuel lines and filters that reduces engine performance. Inspectors verify that the fuel dispensed is clear and bright at ambient temperature and does not contain either of these contaminants. In addition, the presence of water in the fuel storage tanks is also measured.
Phase Separation – With the widespread introduction of ethanol into gasoline roughly 15 years ago the problem of phase separation started to emerge. Unlike conventional or non-ethanol gasoline, the presence of ethanol allows the fuel to absorb a small amount of water with no effect. However, since ethanol is more chemically similar to water than the hydrocarbon components of gasoline, once the maximum amount of water is absorbed, any additional water added will result in the water stripping the ethanol out of the gasoline. What is left is a solution that has two distinct layers; a mixture of ethanol and water sits at the bottom of the tank and an ethanol depleted gasoline layer floats on top. This ethanol and water mixture is very caustic and, in some cases, can lead to engine damage. Inspectors visually inspect gasoline samples for the presence of phase separation and also check the storage tanks for its presence. Under current North Carolina code, the presence of phase separation in a storage tank is grounds for closure of the dispensed fuel product even if phase separation is not found coming through the dispenser. Samples are collected directly from the storage tank using a bacon bomb, that allows us to collect product on the bottom of the tank, where any water or phase separation may be.
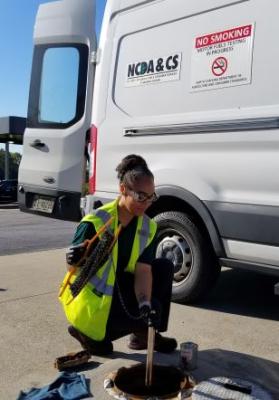
Diesel, Biodiesel blends, and Kerosene
Flashpoint – The flashpoint is the temperature at which there are enough vapors above a liquid to support the combustion when a flame is introduced. This test is important in determining if a fuel is safe to use or if it contains a lower boiling fuel such as gasoline. The presence of gasoline in diesel or kerosene can lead to significant engine damage or a potential fire if used in a home heater. Inspectors check the flashpoint of all diesel and kerosene products offered for sale using a manual flashpoint unit following ASTM test method D56.
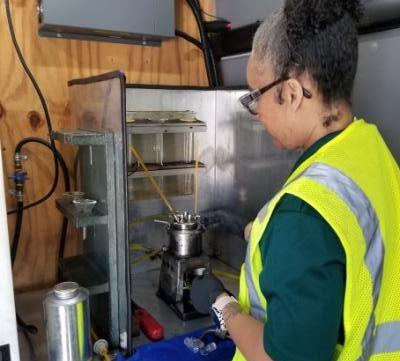
Water and Sediment – Water is the largest concern for consumers when it comes to fuel quality as its presence can result in poor performance and possible engine failure. Sediment is a growing concern as more diesel engines shift to utilize high pressure fuel systems and, in some cases, the presence of this contaminant can result in significant damage to fuel delivery systems. Inspectors verify that the fuel dispensed is clear and bright at ambient temperature and does not contain either of these contaminants. In addition, the presence of water in the fuel storage tanks is also measured.